The producing process of all types of cans, profiles and tubes (cold rolled)
First, the raw materials entered into the factory roller and prepared by the jigging devices according to the cross-sectional production plan and then being prepared as a hinge for the transfer to production lines. The cut pieces of steel are removed from the warehouse and entered into a forging machine. In this step, the forming machine bridges the steel strip edges through horizontal and vertical rollers in several steps. After passing the shaping step of steel strip edges by electric welding which is the most important and most sensitive stage of production, by aid a high frequency without any external material, the melting point is welded to one another. The product being produced is continuously introduced into a sizing machine so that it passes through the horizontal and vertical rollers and then after several stages of conversion, they turn into desired products. The product was transferred to the automatic sawing machine after leaving the cutter and according to the program given to the device; the desired length would cut off. In the complementary stages, the products are transported to the unit for carrying out the operation, and then packaged in accordance with the type of product, if they require the need for polishing and non-destructive testing tests (hydrated and non-destructive tests).
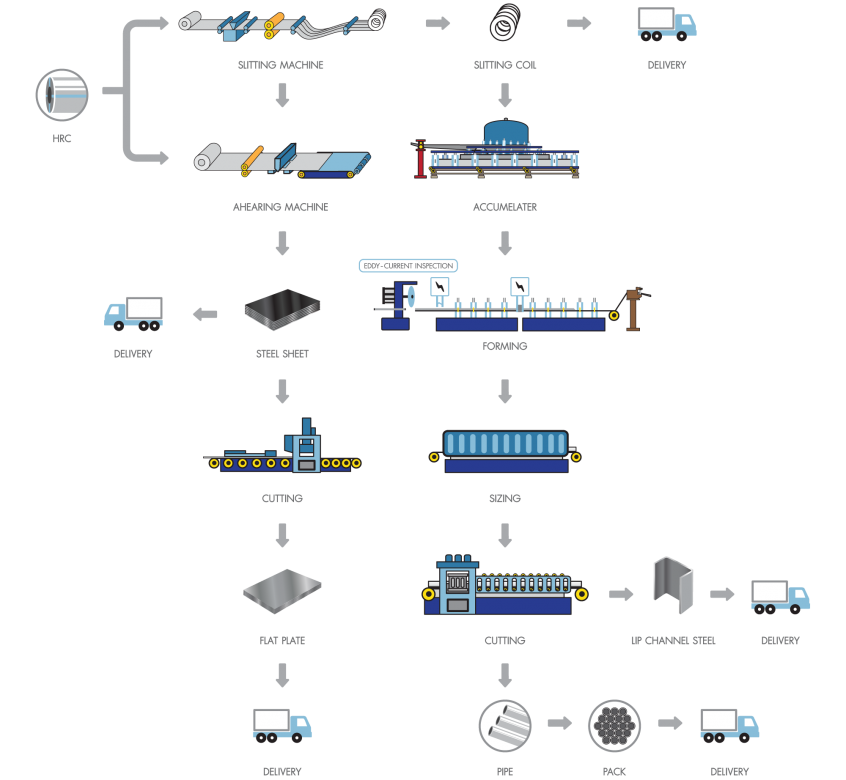
The producing process of beam, corners, studs and fittings (Hot rolled)
At first, the ingots must be introduced into furnaces, which have a furnace temperature of up to 1100 ° C. For this purpose, however, the ingots are guided by a hydraulic jack in specified rows into the furnaces, and when the ingots are placed inside the furnace, they are prepared for rolling by 1100 ° C.
Once the ingots reach the desired temperature, they are sent to the production line, and then the billets are placed on the rolls and directed to the Ruffing stage. At Ruffing stage and in three steps, the diameter of the ingots decreases and the length increases. After the Ruffing stage, there are rolling shelves which range from 10 to 18 in calibers. In the last step of rolling, the scissors area is used to cut products manufactured at specified lengths. Then the products are cut into 12 meter long and at the last stage, they are packed in kind-bundles with a specified weight.
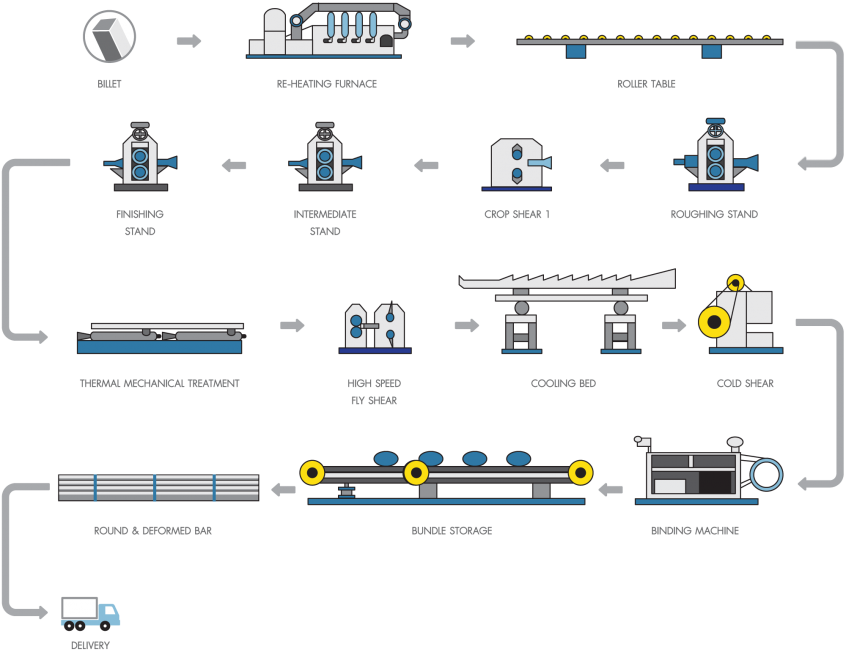